Troubleshooting and Fixing Common Welding Issues
Even the most experienced welders run into issues from time to time.
Whether working on a large-scale structural project or fabricating in a shop, welding problems can cost time, material, and money.
Fortunately, many welding issues are preventable or easily fixed once you know what to look for.
In this post, we'll discuss some of the most common problems welders face and offer practical tips for troubleshooting and resolving them.
Whether you manage a welding team or work solo, we are here to help you improve weld quality and keep your projects on track.
Understanding the Basics Before You Troubleshoot
Before tackling specific problems, it's essential to ensure a solid foundation.
Always confirm that you're using the proper process (MIG, TIG, Stick) for the job and double-check your machine settings, consumables, and shielding gas.
Contaminated materials, incorrect filler metals, or improper technique can all lead to avoidable issues.
Also, don't overlook safety—wear the correct personal protective equipment (PPE), and ensure your workspace is well-ventilated.
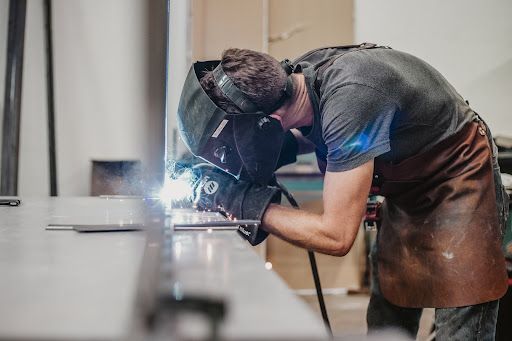
Common Welding Issues and How to Troubleshoot Them
Porosity (Gas Pockets in the Weld)
Symptoms: Tiny holes or cavities in the weld bead that weaken the joint.
Causes:
- Dirty or rusty base metal
- Contaminated shielding gas
- Moisture in the electrode or filler wire
Fixes:
- Thoroughly clean the metal before welding
- Check for leaks in gas lines and ensure proper gas flow
- Store consumables in a dry, temperature-controlled environment
Incomplete Fusion
Symptoms: The weld bead does not fully bond with the base metal, leading to weak joints.
Causes:
- Insufficient heat input
- Fast travel speed
- Incorrect electrode angle
Fixes:
- Increase amperage or voltage settings
- Slow down travel speed slightly
- Adjust your torch or electrode angle to maintain better contact
Cracks
Symptoms: Cracks that appear either during or after welding, often starting at the weld toe or root.
Causes:
- Rapid cooling, especially on thick materials
- Contaminated base metal
- Poor joint design or fit-up
Fixes:
- Preheat thicker materials as needed
- Clean the joint thoroughly before welding
- Design joints that distribute stress more evenly
Undercut
Symptoms: A groove melted into the base metal along the weld toe, which can reduce strength.
Causes:
- Too high amperage
- Poor torch manipulation
- Fast travel speed
Fixes:
- Lower the amperage to appropriate levels
- Maintain a steady hand and consistent electrode angle
- Slow down your travel speed just enough to allow proper filling
Spatter
Symptoms: Small droplets of molten metal that scatter and stick to the work surface.
Causes:
- Excess voltage
- Incorrect wire feed speed
- Poor gas coverage
Fixes:
- Adjust voltage and wire speed settings to recommended levels.
- Inspect and clean the nozzle and contact tip regularly.
- Use anti-spatter sprays or gels for cleaner results.
Machine-Related Troubleshooting Tips
Sometimes the issue isn't with your technique or materials—it's the machine.
Here are a few quick things to check:
- Cables and connections: Loose or frayed wires can cause irregular arc behavior.
- Ground clamps: A poor ground connection can cause arc instability.
- Consumables: Replace worn-out contact tips, nozzles, and liners regularly.
- Wire feed system: Look for tangles, kinks, or inconsistent feeding.
Routine maintenance and inspections go a long way toward preventing downtime.
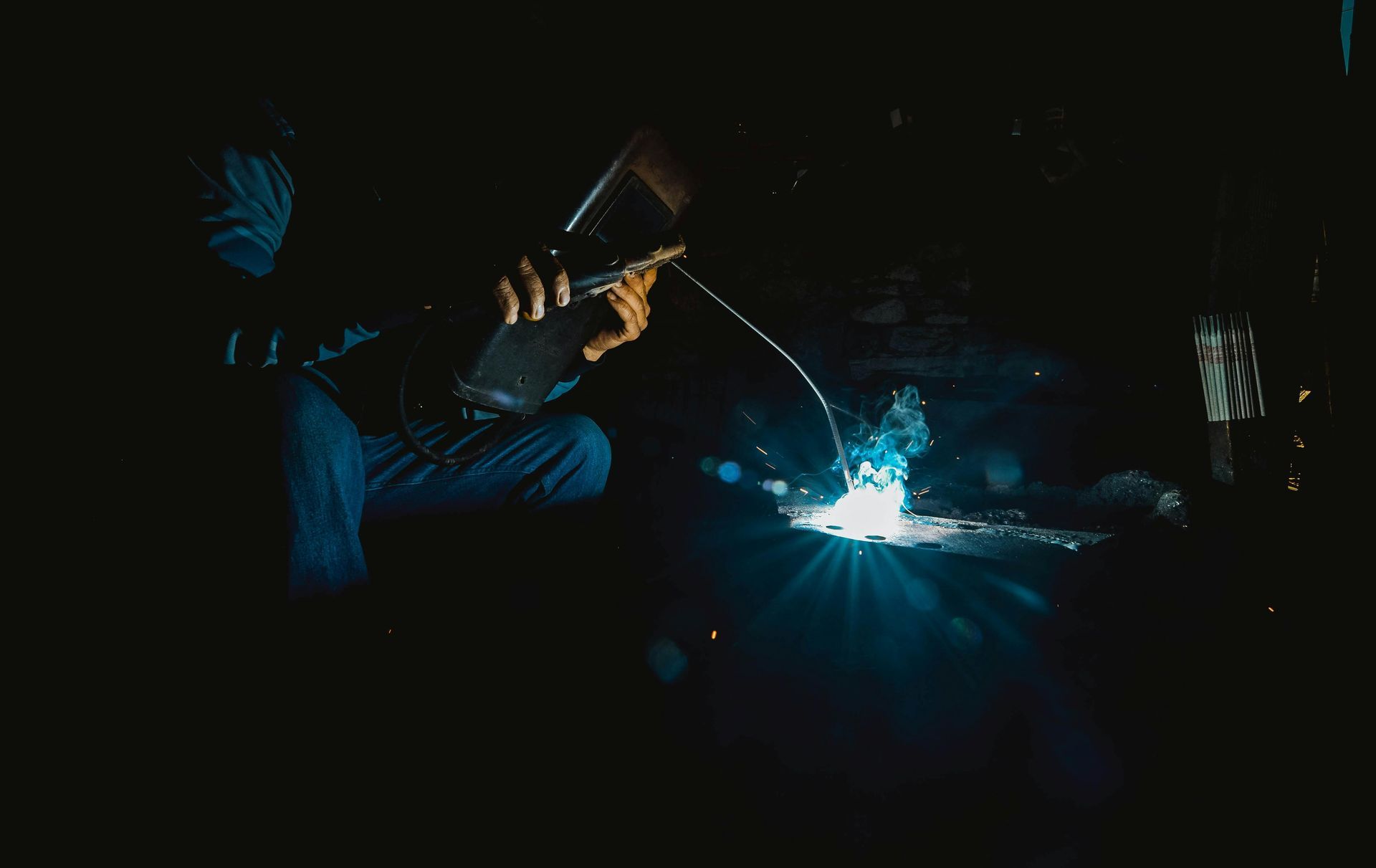
Material-Specific Troubleshooting
Different base materials come with their unique challenges:
- Carbon Steel: Tends to be more forgiving but needs proper prep to avoid porosity and cracking.
- Stainless Steel: Sensitive to heat input; improper technique can cause warping or discoloration.
- Aluminum: Highly conductive and prone to oxidation—requires clean surfaces and the right filler metal.
Ensure you're using the appropriate shielding gas and filler for the material you're working with, and consider preheating or adjusting travel speed as needed.
When to Call for Help
If you've gone through all the steps and still can't figure out what's wrong, it might be time to reach out for support.
Machine malfunctions, hidden material flaws, or complex joint designs may require the insight of a welding technician or supplier rep.
Welding issues happen, but knowing how to spot and fix them quickly separates good welders from great ones.
Keep your workspace clean, your equipment maintained, and your settings dialed in—and always be ready to adjust based on what you see.
Work With KDAR Company
Here at KDAR Company, we take seriously our role as a wholesaler of welding equipment, cable ties, and other related products.
Our retailers can trust us to provide dedicated service and industry expertise.
Contact us today to learn more about our offerings or to let our experts help you source the right equipment for your next project!