Welding Mistakes To Watch Out For
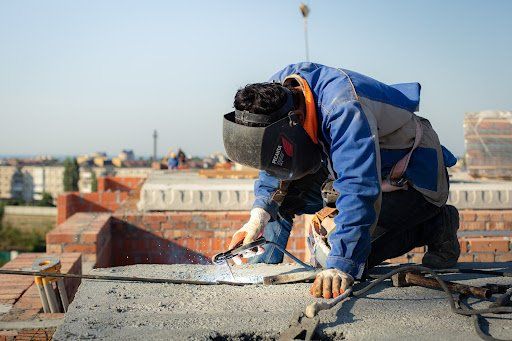
Mistakes are opportunities to learn and grow in skill, but at their worst, a mistake can lead to an injury or a significant issue. Mistakes can (and will) happen in every industry and occupation. However, a mishap in a welding project can quickly cause problems, and unfortunately, there's no giant eraser to come along and get rid of these slip-ups. The best way to avoid mistakes in welding is to keep up with continuous training and learn from any previous mishaps.
The Impact of Outdated Equipment and Incorrect Usage
Using outdated welding equipment can have far-reaching consequences for your projects. Older machinery may lack the advanced features that ensure efficient and precise welding. Inefficient equipment can result in time-consuming rework, increased material waste, and reduced productivity.
To avoid these issues, it's crucial to regularly update your equipment to stay current with the latest welding technologies. Additionally, misusing welding equipment can lead to a host of problems. Poor weld quality, unstable arcs, and inadequate penetration are just a few of the issues that can arise. Always familiarize yourself with the manufacturer's guidelines and proper usage techniques for each piece of equipment.
The Right MIG Gun Size Matters
Choosing the appropriate MIG gun size is a critical aspect of successful welding. MIG guns that are too small might not provide sufficient power, leading to incomplete welds. On the other hand, using a MIG gun that is too large can result in excessive heat and potential distortion of the material you are welding.
To determine the right MIG gun size for your application, consider the type of welding you're doing and the thickness of the materials involved. Consult with welding professionals or refer to the equipment's documentation for guidance on selecting the proper gun size. This minor adjustment can significantly affect the quality of your welds.
Ensuring Proper PPE
Safety should always be a top priority in welding. Personal Protective Equipment (PPE) is crucial in shielding welders from potential hazards. Proper welding helmets, gloves, and flame-resistant clothing are essential to protect against burns, sparks, and harmful fumes.
Selecting the appropriate PPE is not a one-size-fits-all endeavor. Assess the specific welding tasks you'll be performing and the associated risks. Invest in high-quality PPE that offers comfort and protection, and make it a non-negotiable part of your welding routine.
Preheat and Interpass Temperature Control
Welding involves the precise manipulation of temperature to create strong and durable bonds. Neglecting preheating or interpass temperature control can result in structural weaknesses, cracks, and incomplete fusion. It's crucial to adhere to recommended temperature guidelines to achieve optimal weld quality.
Before beginning your weld, ensure the preheat temperature is appropriate for the materials you plan to join. Likewise, maintain consistent interpass temperatures to avoid rapid cooling that can lead to cracks and defects. By paying attention to temperature control, you'll enhance your welds' overall strength and integrity.
Addressing Storage and Maintenance Issues
Practical welding goes beyond the actual act of welding; it extends to proper equipment care and storage. Improperly storing welding equipment can lead to moisture contamination, rusting, and premature deterioration. To protect your investments, create a dedicated storage area that's dry and well-ventilated.
Keep welding consumables and equipment in their original packaging whenever possible. Seal containers tightly to prevent moisture intrusion. Regularly inspect stored items for signs of damage or degradation, and replace any compromised materials promptly. Maintaining a well-organized storage system will extend the lifespan of your equipment and materials.
Regular Equipment Maintenance for Longevity
Welding equipment is an investment that requires ongoing care to ensure longevity and optimal performance. Neglecting routine maintenance can lead to decreased efficiency, increased downtime, and costly repairs. By contrast, consistent upkeep can prevent unexpected breakdowns and extend the life of your equipment.
Create a maintenance schedule that includes cleaning, inspecting, and lubricating equipment components. Address any issues promptly to prevent them from escalating into major problems. Regularly calibrate your equipment to ensure accurate performance and reliable results. With proactive maintenance, you'll experience smoother welding operations and fewer disruptions.
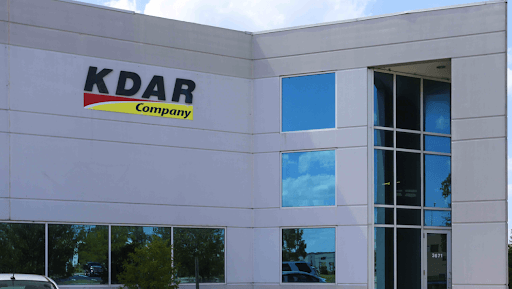
Work With KDAR Company
Avoiding common mistakes is critical to achieving high-quality, safe, and efficient results in welding. KDAR Company understands welders' challenges, so we provide top-tier welding equipment and supplies to support your endeavors. By staying up-to-date with industry best practices, embracing proper equipment usage, and adhering to safety protocols, you can ensure that your welding projects are a testament to precision and excellence. Remember, welding is both an art and a science, and by arming yourself with knowledge, you're paving the way for welding success. Contact us today!